過去25年間にわたり、ダイニーマ®は優れた特性のおかげでリスクの高い業界で不可欠な存在となってきました。
ダイニーマ®はUHMPE繊維として始まりました。
この超高分子量ポリエチレン繊維はオランダのDSMと東洋紡が1984年から共同研究を開始し、事業化したものです。
日本での生産は、1991年からDSMダイニーマと東洋紡の合弁会社である日本ダイニーマ(日本では非上場会社だと思います⇒大株主になろうとして調べました)が行っており、東洋紡が「イザナス®」のブランドで販売しています。なお、DSMはこの繊維を「ダイニーマ®」のブランドで生産販売しています。
近年では、多数の中国メーカーも超高分子量ポリエチレン繊維の生産に乗り出しており、世界全体での生産能力は3万トン以上あると推定されています。
このイノベーションとコラボレーションを通して、用途が広がっただけでなく、ファイバーから単方向シート、ファブリックにいたるまで、様々な形態でも利用できるようになりました。 これらの形態はすべて、 以下 のような優れた性質を備えています。↓![]()
究極のフライト体験パラグライディングは、自由に飛びたいという人類の最古の夢をかなえる最もシンプルかつ平穏な方法です。重要なのは腕前と平静さです。完全に装備に依存しなくてはなりません。パラグライディング用ラインでダイニーマ®を使用すると、極めて軽く細いラインになるため、最高のパラグライディングを体験できます。
↓重量に対して超高強度(同一重量比で強度はスチールの15倍=引張り強さは最高43 cN/dtexで水に浮きます)![]()
低い破断時の伸び率高い紫外線耐性![]()
高い耐薬品性浮遊性高い柔軟性高いエネルギー吸収(衝撃吸収性)&耐久性⇒#TIMEには最適な素材です!無限大位な勢いです。
「高い靭性」(じんせい)とは、構造物や素材または部材の強度、ねばり強さのこと。 外部からの圧力に対して耐えられる抵抗の程度や、あるいは部材に亀裂が生じているときの抵抗の程度。 「靭性」の高い部材は、圧力に対して破壊されづらい為、例えば建物の部材に対して「靭性」が試されまする。カーボン繊維の0に対しダイニーマ®SK60は12~20cN/dtexあります。他の繊維に対しても10~100倍強いという事です。においや味はなし、無毒性低摩擦で自己潤滑性そして25年の歳月を費やし、ようやくフレームの素材として活用できるようになりました。なぜなら弱点があったからです。融点が150℃と低いため、耐熱性が求められる用途には使えません。他社でよく使われるカーボンプリプレグは、130℃硬化型であったり、用途によっては180℃硬化型も使います。 加工温度を130℃とすれば数時間の熱履歴でも強度は80%以上保持されます。耐熱性はダイニーマの唯一の短所です!専門的になり過ぎましたが#TIMEのRTM工法だけが自転車フレームの中でダイニーマ®を使えるという事です。↓![]()
バイオベースのダイニーマファイバー↓![]()
近年、ダイニーマは自転車業界からもっとも注目を集めた素材の1つです。この超高分子量ポリエチレンは耐衝撃性、耐引裂強度に優れた強靱な素材で、シューズやバッグのベース素材として使われました。しかし、実際の製品に応用したメーカーは多くありません。(コストが高い為)また、ダイニーマは耐熱性に弱点を抱えるため、汎用的なプリプレグ構造のフレームでは採用できないからです。 タイムは違います。
自社で独自に繊維を編み込むため、DSM社からダイニーマがリリースされた直後からテストすることができました。RTM工程では樹脂の温度が低いため、ダイニーマを採用することもできます。![]()
↓★特質は?カーボンとバイオベースのダイニーマ繊維を組み合わせて編み込むことで、ADHXは剛性や重量への悪影響なく強度を高めることができます。
★どの部分にどれだけ使いますか?ヘッドチューブ、ダウンチューブ、トップチューブが交差する箇所に使います。重量比でダイニーマを20~25%使用しています。
★なぜ内部のみに使うのですか?繊維に負荷がかかった時に、高強度&高弾性なダイニーマの特徴が発揮されます。
衝突して前方から衝撃を受け、構造体の内部に負荷がかかったときも、フレームが破断するリスクが極めて小さくなります。
素材についての説明はこれにて終了とさせて頂きます。明日はフレームの特性や規格も含めて、私がどういうロードレーサーに組みたいか、ご説明させていただきます。m(_ _)m
素材について専門的にお調べになりたい方はこちらをクリックして下さいませ。
↓
https://www.jstage.jst.go.jp/article/fiber/66/3/66_3_P_91/_pdf↓

この超高分子量ポリエチレン繊維はオランダのDSMと東洋紡が1984年から共同研究を開始し、事業化したものです。
日本での生産は、1991年からDSMダイニーマと東洋紡の合弁会社である日本ダイニーマ(日本では非上場会社だと思います⇒大株主になろうとして調べました)が行っており、東洋紡が「イザナス®」のブランドで販売しています。なお、DSMはこの繊維を「ダイニーマ®」のブランドで生産販売しています。
近年では、多数の中国メーカーも超高分子量ポリエチレン繊維の生産に乗り出しており、世界全体での生産能力は3万トン以上あると推定されています。
このイノベーションとコラボレーションを通して、用途が広がっただけでなく、ファイバーから単方向シート、ファブリックにいたるまで、様々な形態でも利用できるようになりました。 これらの形態はすべて、 以下 のような優れた性質を備えています。↓
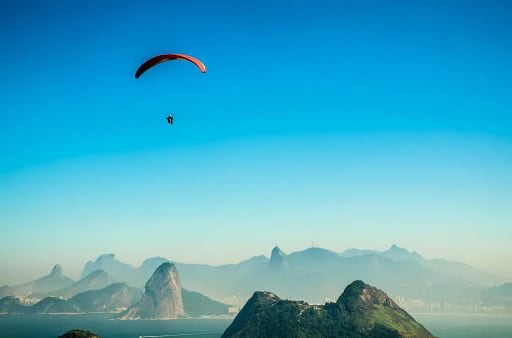
究極のフライト体験パラグライディングは、自由に飛びたいという人類の最古の夢をかなえる最もシンプルかつ平穏な方法です。重要なのは腕前と平静さです。完全に装備に依存しなくてはなりません。パラグライディング用ラインでダイニーマ®を使用すると、極めて軽く細いラインになるため、最高のパラグライディングを体験できます。
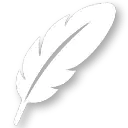
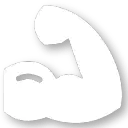
低い破断時の伸び率高い紫外線耐性
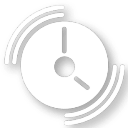
高い耐薬品性浮遊性高い柔軟性高いエネルギー吸収(衝撃吸収性)&耐久性⇒#TIMEには最適な素材です!無限大位な勢いです。


バイオベースのダイニーマファイバー↓
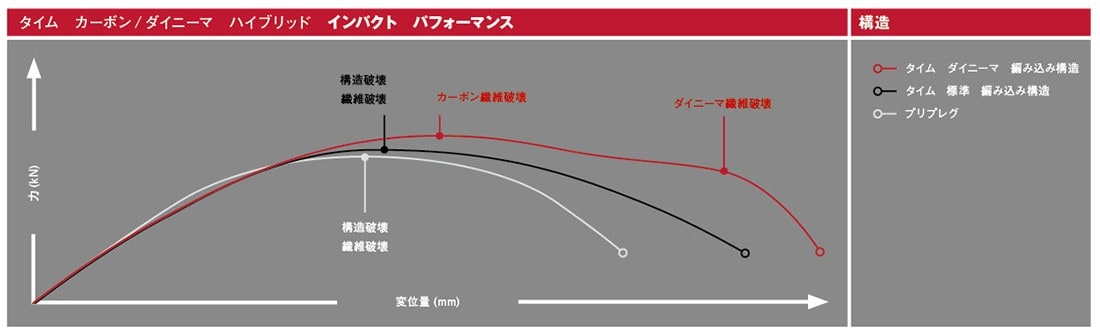
近年、ダイニーマは自転車業界からもっとも注目を集めた素材の1つです。この超高分子量ポリエチレンは耐衝撃性、耐引裂強度に優れた強靱な素材で、シューズやバッグのベース素材として使われました。しかし、実際の製品に応用したメーカーは多くありません。(コストが高い為)また、ダイニーマは耐熱性に弱点を抱えるため、汎用的なプリプレグ構造のフレームでは採用できないからです。 タイムは違います。
自社で独自に繊維を編み込むため、DSM社からダイニーマがリリースされた直後からテストすることができました。RTM工程では樹脂の温度が低いため、ダイニーマを採用することもできます。
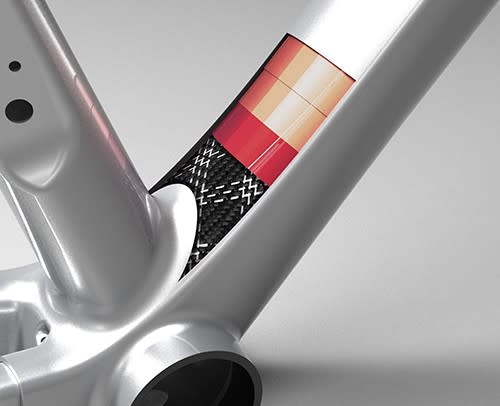
↓★特質は?カーボンとバイオベースのダイニーマ繊維を組み合わせて編み込むことで、ADHXは剛性や重量への悪影響なく強度を高めることができます。
★どの部分にどれだけ使いますか?ヘッドチューブ、ダウンチューブ、トップチューブが交差する箇所に使います。重量比でダイニーマを20~25%使用しています。
★なぜ内部のみに使うのですか?繊維に負荷がかかった時に、高強度&高弾性なダイニーマの特徴が発揮されます。
衝突して前方から衝撃を受け、構造体の内部に負荷がかかったときも、フレームが破断するリスクが極めて小さくなります。
素材についての説明はこれにて終了とさせて頂きます。明日はフレームの特性や規格も含めて、私がどういうロードレーサーに組みたいか、ご説明させていただきます。m(_ _)m
素材について専門的にお調べになりたい方はこちらをクリックして下さいませ。
↓
https://www.jstage.jst.go.jp/article/fiber/66/3/66_3_P_91/_pdf↓